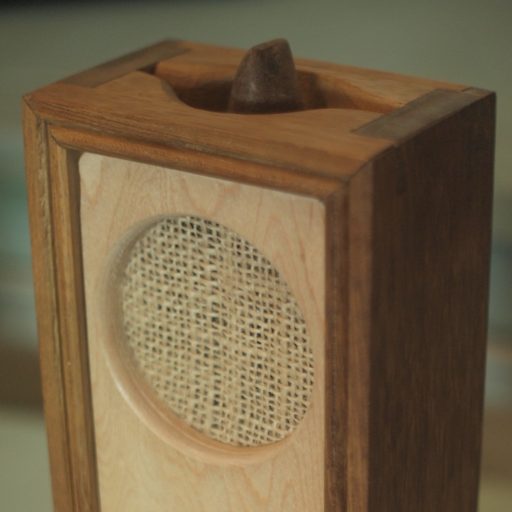
JCP DesignHandmade furniture and technology in wood
© 2008 - 2020 JCP Design
© 2008 - 2020 JCP Design
Since 2008 I’ve been working on various handmade speaker designs, from monstrous surround sound setups, to mixing monitors, to battery powered portables and as many in between as I could think of.
With a Masters Degree in Product Design Engineering from the Glasgow School of Art and The University of Glasgow, I had a good foundation in design and engineering. Along the way I built up my woodworking skills, moving back home to Dorset and learning traditional woodworking skills at The Boat Building Academy in Lyme Regis.
Jonathan Pritchard
My aim is to bring the pasts high quality hand joinery to present day items. The art is not lost quite yet and I believe there is still a place for hand made objects made to be used and made to last. Now more than ever with sustainability becoming more important.
Come visit the shop!
Unit 100
St Michaels Trading Estate
Bridport
Dorset
DT6
Opposite Bridport Bus station.